The Ultimate Guide to PLC Maintenance for Businesses
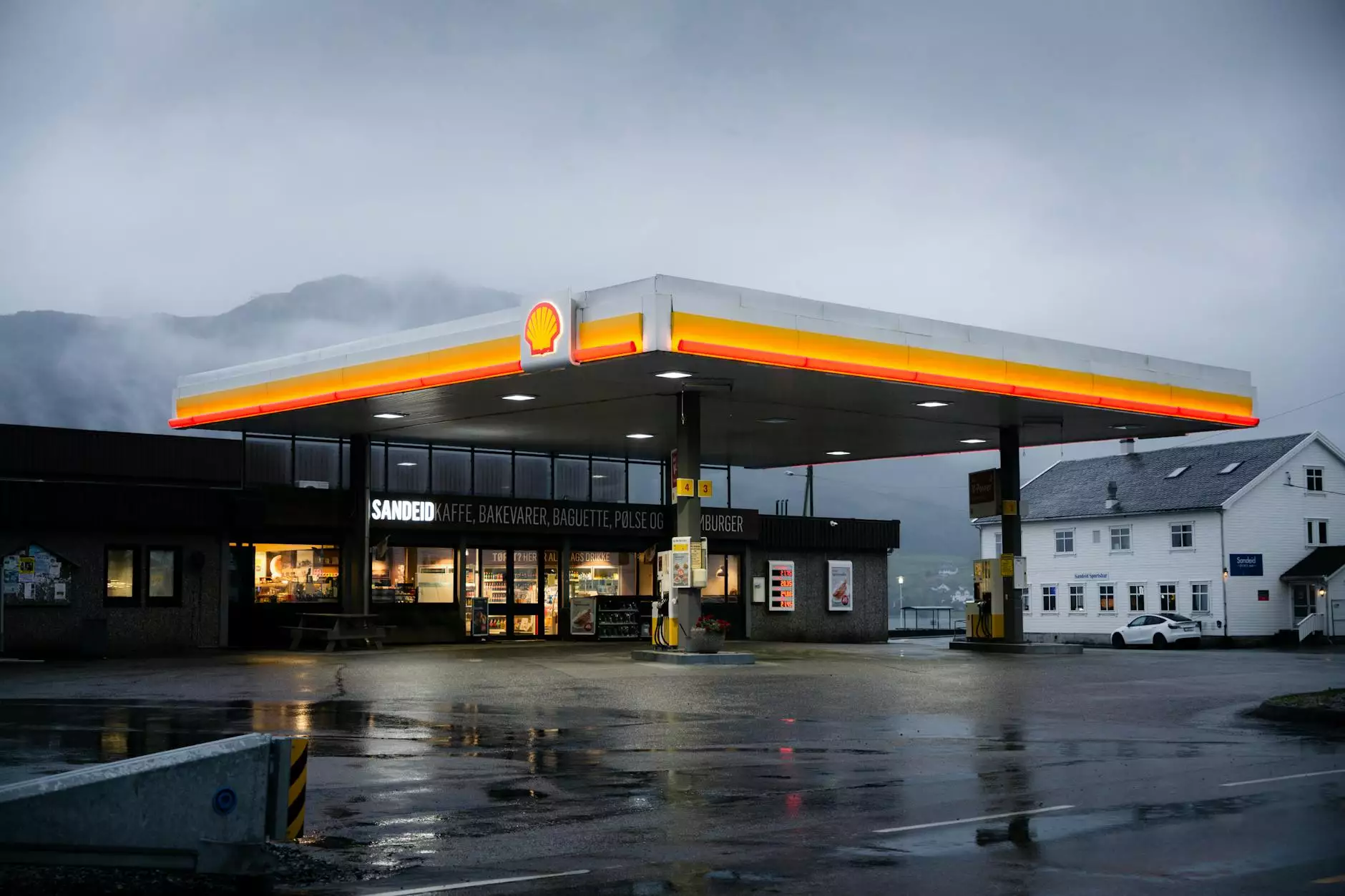
In today’s technologically advanced world, mastering the intricacies of PLC maintenance is crucial for businesses operating in the automation and control systems industry. As Programmable Logic Controllers (PLCs) become integral to various industrial applications, the demand for reliable maintenance services has surged. This comprehensive guide is designed to provide you with valuable insights into PLC maintenance, ensuring your systems operate optimally and your business continues to thrive.
Understanding the Role of PLCs in Modern Business
PLCs are digital computers used for automation of electromechanical processes. These include control of machinery on factory assembly lines, amusement rides, lighting systems, and other applications that require high reliability and ease of programming and process fault diagnosis. Their significance in manufacturing cannot be overstated, especially in Canada’s dynamic industrial landscape.
Key Functions of PLCs
- Real-Time Processing: PLCs handle real-time operations, enabling systems to respond immediately to changing conditions.
- Robust Control: They provide precise control of various manufacturing processes, minimizing errors and waste.
- Interfacing Capabilities: PLCs can interface with various sensors, actuators, and other hardware, facilitating a comprehensive automation system.
The Importance of PLC Maintenance
Like any other machinery, PLCs require regular maintenance to ensure longevity and efficiency. PLC maintenance is not just a recommendation; it is a necessity. Neglecting regular upkeep can lead to costly downtimes and significant operational disruptions.
Benefits of Regular PLC Maintenance
- Extended Equipment Lifespan: Regular maintenance can significantly enhance the lifespan of your PLC, reducing the need for expensive replacements.
- Improved Reliability: Frequent checks help identify potential failures before they happen, ensuring uninterrupted production processes.
- Enhanced Performance: Over time, systems can lose efficiency. Maintenance ensures that PLCs work at their optimal level.
Common Issues That Require PLC Maintenance
Understanding common PLC issues can help businesses prioritize their maintenance efforts. Here are some typical problems encountered:
1. Hardware Failures
Hardware failures can occur due to electrical surges, overheating, and component wear. Regular inspections can help identify worn-out parts and replace them before they cause failures.
2. Software Glitches
Just like any other computer system, PLCs can experience software glitches. Maintaining updated software and performing regular backups can minimize these risks.
3. Connectivity Issues
As systems grow more complex, connectivity issues may arise. Regular maintenance checks can help ensure that communication between devices is seamless, preventing costly breakdowns.
Best Practices for Effective PLC Maintenance
To maximize the benefits of PLC maintenance, implement these best practices in your organization:
Regular Inspection Routines
Establish a routine inspection schedule to check for signs of wear, loose connections, and dust accumulation. A clean and well-organized control panel is crucial for effective monitoring and operation.
Documentation
Maintain detailed logs of all maintenance activities. This documentation should include inspection dates, issues found, actions taken, and any parts replaced. Proper records facilitate better decision-making regarding future maintenance strategies.
Training and Development
Invest in training your staff on PLC operation and maintenance. A well-informed team can handle minor problems before they escalate into serious issues, ensuring that systems remain operational.
Choosing the Right PLC Maintenance Service Provider
Your choice of a maintenance service provider can significantly impact the efficiency of PLC maintenance. Here are some factors to consider when selecting a partner:
Experience and Expertise
Choose a provider with a proven track record in PLC maintenance. Check for certifications, client testimonials, and case studies to gauge their expertise.
Comprehensive Services
Look for a service provider that offers a range of services, including repair, replacement, and emergency support. This ensures that you have access to a complete solution for all your PLC needs.
Timeliness and Availability
In the event of a failure, timely support is critical. Ensure that your service provider can offer prompt assistance and is available during business hours, as well as for emergencies.
Exploring QF Automation’s PLC Maintenance Services
As a leading electronic components distributor in Canada, QF Automation offers a comprehensive suite of services tailored to meet your PLC maintenance needs. Here’s what we provide:
Expert Repairs
Our skilled technicians specialize in PLC repair services, equipped with the knowledge to resolve issues efficiently and effectively. We understand the intricacies of various PLC brands and models, ensuring reliable service tailored to your requirements.
Parts Distribution
We stock a wide range of electronic components, ensuring that you have access to the parts needed for quick repairs. Our extensive network allows us to source hard-to-find components, minimizing downtime.
Consultation Services
Our experts are available for consultation, providing you with insights into optimizing your PLC systems for better performance. We perform in-depth assessments of your current systems and recommend actionable solutions.
Future of PLCs and Maintenance Practices
The future of PLCs is promising, with advancements in technology paving the way for even more reliable and efficient systems. As the demand for automation grows, so does the necessity for effective PLC maintenance practices. Businesses that invest in their maintenance strategies will reap significant rewards, including increased productivity and reduced operational costs.
Emphasis on Preventative Maintenance
Moving forward, the industry will likely shift towards a more proactive approach to maintenance, focusing on predictive analytics and intelligent monitoring systems. Implementing such technologies can help foresee potential issues before they impact productivity.
Conclusion
In conclusion, understanding and implementing effective PLC maintenance is essential for any business relying on these systems for automation. From extending your equipment's lifespan to enhancing overall operational efficiency, the benefits are undeniable. By prioritizing maintenance and partnering with reputable service providers like QF Automation, you can ensure that your PLC systems remain reliable and efficient, ready to meet the demands of an ever-evolving industrial landscape.
Take the first step towards ensuring the reliability of your systems by exploring QF Automation’s dedicated services today.