Understanding the Electric Plastic Injection Moulding Machine: A Key Asset for Metal Fabricators
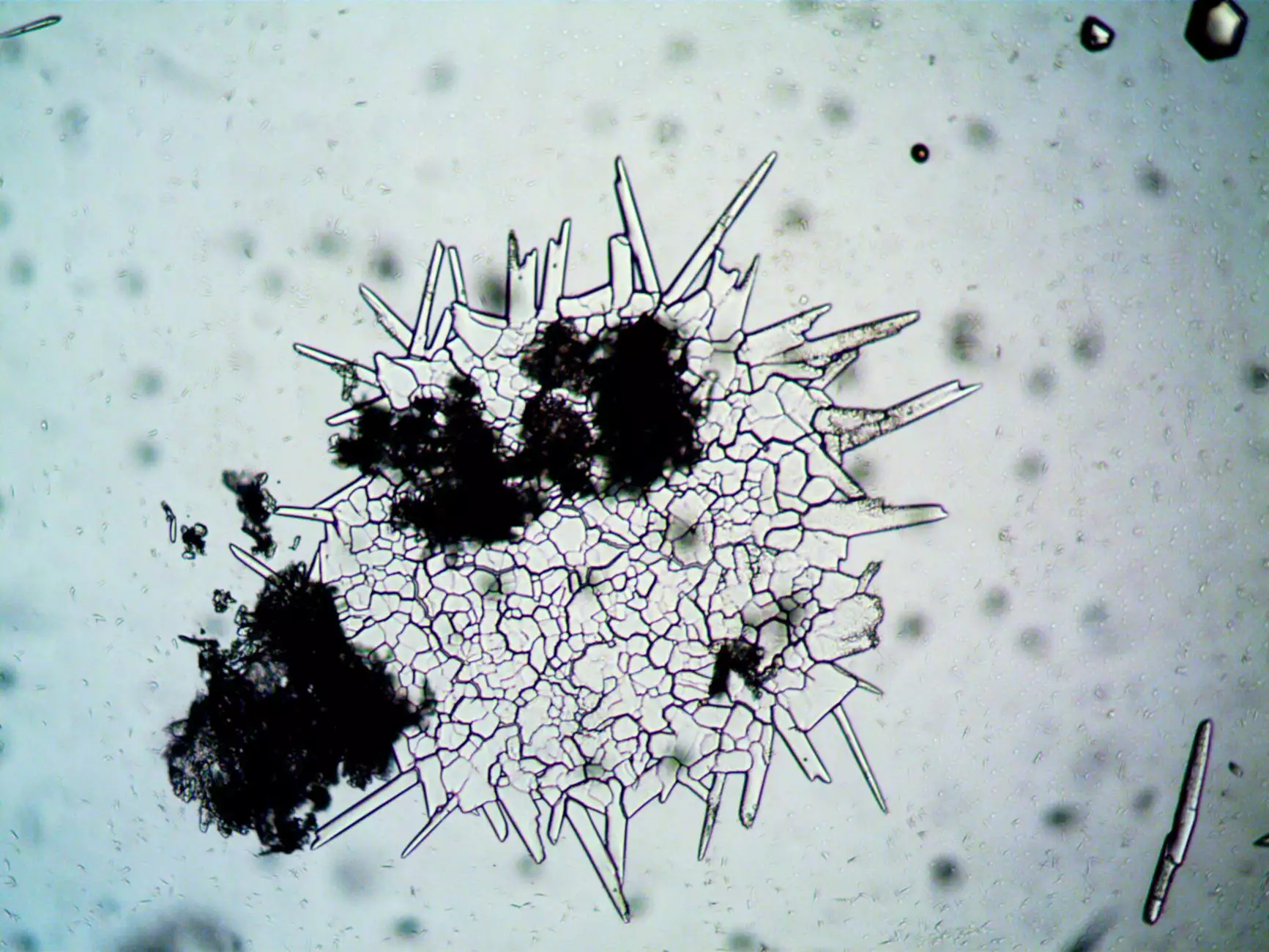
The Electric Plastic Injection Moulding Machine is revolutionizing the way businesses in the metal fabrication industry operate. With advancements in technology and a growing emphasis on efficiency and sustainability, these machines are rapidly becoming indispensable. This article delves deep into the workings, benefits, and applications of Electric Plastic Injection Moulding Machines, specifically within the context of the metal fabricators sector.
What is an Electric Plastic Injection Moulding Machine?
An Electric Plastic Injection Moulding Machine is a type of manufacturing equipment that uses electrical power to inject molten plastic into a mold cavity, where it cools and solidifies to form a specific shape. Unlike their hydraulic counterparts, which rely on hydraulic fluids for operation, electric moulding machines provide precise control over the injection process, yielding high-quality products with more intricate designs.
Key Components of Electric Plastic Injection Moulding Machines
- Injection Unit: This unit melts the plastic pellets and injects them into the mould with high pressure.
- Clamping Unit: This component holds the mould in place during the injection process to prevent leakage.
- Control System: The advanced control system allows for precise adjustments to temperature, pressure, and timing, ensuring product consistency.
- Mould: The mould is where the molten plastic takes shape. Custom-built moulds can be used to create complex designs.
Advantages of Electric Plastic Injection Moulding Machines
Electric Plastic Injection Moulding Machines come with numerous advantages that make them a preferred choice among manufacturers.
1. Enhanced Energy Efficiency
One of the most significant benefits of electric machines is their energy efficiency. These machines consume less electricity compared to hydraulic machines, reducing operational costs significantly. This makes them an excellent choice for companies looking to lower their energy bills and minimize their environmental impact.
2. Precision and Consistency
Electric machines offer unparalleled precision in the moulding process. The electronic servo motors provide consistent speed and force, minimizing variations in production. This level of precision is crucial for industries that require high-quality, uniform products.
3. Reduced Maintenance Costs
Electric moulding machines typically have fewer moving parts than hydraulic machines, leading to lower maintenance costs. The absence of hydraulic fluids reduces the risk of leaks, further enhancing machine longevity and reliability.
4. Faster Cycle Times
Due to their quick response times and efficiency, electric machines can achieve faster cycle times, increasing overall production capacity. This speed can provide a competitive edge, allowing businesses to meet customer demands promptly.
Applications of Electric Plastic Injection Moulding Machines in Metal Fabrication
The versatility of Electric Plastic Injection Moulding Machines allows them to be utilized in various applications within the metal fabrication industry. Some notable applications include:
1. Production of Complex Components
When it comes to producing intricate components that require fine details, electric machines shine. They can create complex shapes that are often needed in industries such as aerospace, automotive, and electronics. These industries regularly demand high-performance components that can withstand rigorous conditions, and electric moulding machines can deliver precisely that.
2. Custom Moulding Solutions
Metal fabricators often require custom solutions tailor-made to specific project needs. Electric moulding machines can easily adapt to different kinds of plastic materials, allowing for custom moulding solutions that cater to diverse production needs. This adaptability enhances the capacity of manufacturers to provide bespoke services to their clients.
3. Prototyping and Sample Production
Before mass production begins, companies often create prototypes to test ideas and designs. Electric plastic injection moulding machines are ideal for prototyping due to their precision and ability to switch between different designs quickly. This process speeds up the development phase, allowing businesses to refine their products efficiently.
Why Choose Electric Plastic Injection Moulding Machines?
The choice between electric and hydraulic moulding machines can significantly impact a company's productivity and profitability. Here’s why opting for Electric Plastic Injection Moulding Machines can be profoundly beneficial:
1. Environmental Sustainability
With more businesses committing to sustainable practices, electric machines stand out due to their lower carbon footprint. They produce fewer emissions and use less energy, aligning with global sustainability goals.
2. Quality Improvements
As mentioned, electric moulding machines provide better control over the production process, which translates into higher-quality products. This improvement can lead to fewer defects and reworks, saving time and money in the long run.
3. Long-Term Cost Savings
While the initial investment in electric moulding machines might be higher than hydraulic alternatives, the long-term cost savings gained from reduced energy consumption, lower maintenance, and higher production efficiency make them a prudent financial choice for fabricators.
Conclusion
In the fast-paced world of metal fabrication, leveraging advanced technologies such as the Electric Plastic Injection Moulding Machine not only enhances productivity but also aligns with modern standards of sustainability and efficiency. With their numerous benefits, including energy efficiency, precision, lower maintenance costs, and versatility, electric moulding machines have established themselves as invaluable assets for businesses in this sector. As industries continue to evolve, the adoption of innovative manufacturing technologies will be critical in maintaining competitive advantage, ensuring that businesses can meet the growing demands of the market while also protecting our planet.
As businesses explore the potential of electric moulding technology, they will find that not only do these machines provide exceptional efficiency and reliability, but they also enhance their ability to innovate and deliver high-quality products. The trend toward electric plastic injection moulding is not just a passing phase; it is a fundamental shift in how the metal fabrication industry will operate in the coming years.
For more information on how Electric Plastic Injection Moulding Machines can transform your manufacturing processes, visit deepmould.net today.