Understanding Prototype Mold Manufacturers
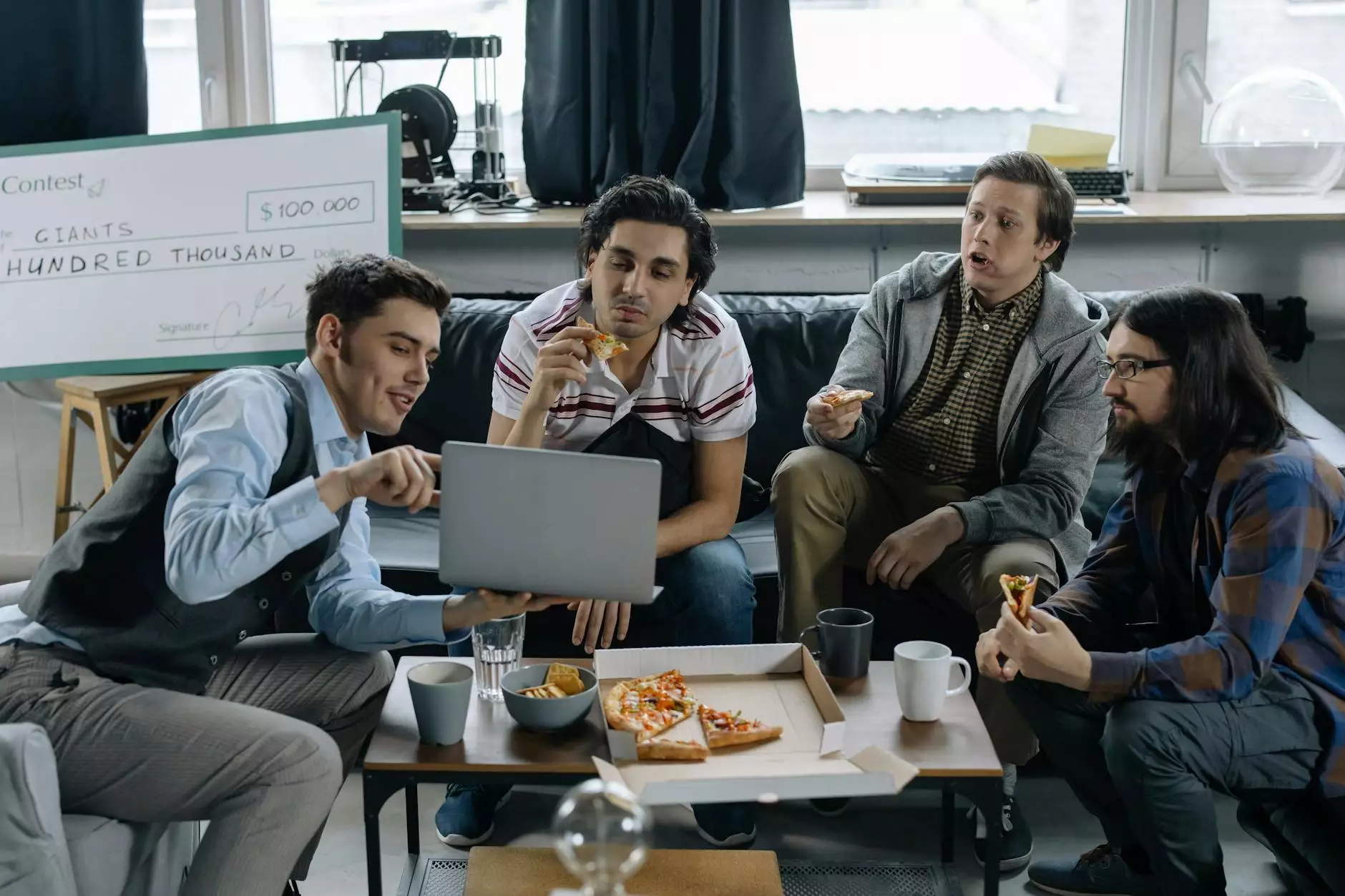
The world of manufacturing is continually evolving, and the role of prototype mold manufacturers is pivotal in this transformation. These specialized companies are at the forefront of innovation, providing essential tools and services for various industries. In this extensive guide, we will delve into the significance of prototype mold manufacturers, their processes, benefits, and much more.
What Are Prototype Molds?
Prototype molds are essential tools in the manufacturing process, specifically designed to create prototypes for new products. They serve as a model or template for mass production. By using prototype molds, businesses can experiment with designs, materials, and functionalities before committing to full-scale production.
Benefits of Using Prototype Molds
- Cost Efficiency: Developing a prototype can significantly cut costs by identifying design flaws early.
- Improved Collaboration: Prototypes foster better communication among designers, engineers, and stakeholders.
- Faster Time to Market: Companies can swiftly go from concept to testing, ensuring they remain competitive.
The Role of Prototype Mold Manufacturers
Prototype mold manufacturers are integral to the production process. Their primary responsibility is to create high-quality molds that meet the precise specifications of their clients. This involves a range of activities, including:
1. Design and Engineering
The first step in the process is designing the prototype mold. This requires expertise in software tools and an understanding of the final product's requirements. Manufacturers often use CAD (Computer-Aided Design) software to develop detailed blueprints.
2. Material Selection
Choosing the right materials is crucial for prototype molds. Common materials include aluminum and steel, known for their durability and performance. The choice depends on factors such as the complexity of the design, the intended use, and budget constraints.
3. Machining and Fabrication
This step involves the actual creation of the mold from the selected materials. Advanced machining techniques, such as CNC (Computer Numerical Control) machining, ensure precision and accuracy in mold fabrication.
4. Testing and Quality Control
Before any mold can be used in production, it must undergo rigorous testing. Prototype mold manufacturers implement strict quality control protocols to guarantee that the mold performs as expected under real-world conditions.
Choosing the Right Prototype Mold Manufacturer
Finding a reliable prototype mold manufacturer can significantly impact your project’s success. Here are some factors to consider when selecting a manufacturer:
1. Experience and Reputation
Look for manufacturers with a proven track record in the industry. Research customer reviews and case studies to assess their reputation.
2. Technological Capabilities
The manufacturing process has become increasingly automated and sophisticated. Ensure that the manufacturer uses advanced technologies to produce high-quality molds efficiently.
3. Customization Options
Your product ideas might need a unique touch. Choose a manufacturer that offers extensive customization options to meet your specific needs.
4. Communication and Support
Effective communication is pivotal in any business relationship. Look for manufacturers that prioritize customer support and maintain open lines of communication throughout the process.
Industries Benefiting from Prototype Mold Manufacturing
The following industries have significantly benefited from prototype mold manufacturing:
- Automotive: Prototyping molds enable car manufacturers to refine parts before large-scale production.
- Consumer Electronics: Rapid prototyping helps electronics companies innovate and quickly iterate designs.
- Medical Devices: Precision molds are essential in creating sterile and functional medical components.
- Packaging: Custom packaging molds ensure products are protected and presented well.
Innovative Trends in Prototype Mold Manufacturing
As industries evolve, prototype mold manufacturers are adopting innovative practices to stay competitive. Here are some key trends:
1. 3D Printing Technology
3D printing has revolutionized prototyping by allowing manufacturers to create accurate molds quickly and cost-effectively. This technology reduces lead times and enhances design flexibility.
2. Sustainable Practices
Environmental sustainability is gaining traction in the manufacturing sector. More manufacturers are adopting eco-friendly materials and processes to minimize waste and energy consumption.
3. Smart Manufacturing
Integrating IoT (Internet of Things) in the production process allows for real-time monitoring and data analysis. This leads to higher efficiency and better resource management.
Conclusion
In summary, the role of prototype mold manufacturers in today’s manufacturing landscape is indispensable. They not only facilitate the development of innovative products but also enhance efficiency, collaboration, and cost-effectiveness. By understanding their processes and the value they bring, businesses can make informed decisions that drive growth and success.
For those looking to partner with a reputable manufacturer, consider visiting deepmould.net, where quality meets innovation in the realm of metal fabrication and prototype molding.